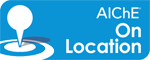
2011 Spring Meeting
Existing processes to produce hydrogen of fuel-cell quality from methane are both capital- and energy intensive, with separate steam reforming (800C), and high-temperature (300C) and low-temperature (200C) water shift reactors necessary to produce acceptable quality hydrogen for use in a Polymer Electrolyte Membrane Fuel Cell (PEMFC). Research is underway in The Netherlands to demonstrate a single palladium membrane reactor (600C) technology to reduce the energy use and cost of small-scale, fuel-cell based electrical power generation. The results generated so far were presented by Fausto Gallucci of theDepartment of Chemical Engineering and Chemistry at the University of Technology, Eindhoven, The Netherlands.
Processes and Results
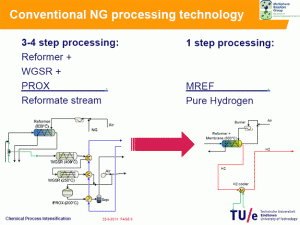
Electrical efficiencies of 34% and fuel efficiencies of 75% are realized with the 3-4 stage process, and the reformate stream to the fuel cell anode is dilute in hydrogen concentration. In the proposed setup, a single fluid-bed membrane reactor is substituted that operates at a lower temperature and produces pure hydrogen for the PEMFC.
Both fixed and fluid-bed reactors were evaluated, with the fixed bed reforming reactor showing significant temperature non-uniformities which resulted in only 75% conversion rates. Utilizing a fluid bed eliminated these inconsistencies in temperature, and thus improved the yields to near 100%.
The Fluid Bed Membrane Reactor (FBMR) system resulted in energy reductions of:
- 50% reduction at the reforming step due to less steam required and lower operating temperatures
- 47% reduction in the fuel processing area due to the reduction in reactor stages and incomplete methane conversion (see trade-offs below), and
- 9% reduction in the actual PEMFC and auxiliary systems due to the pure hydrogen feed from the FBMR
As a result, an electrical efficiency of 43% and fuel efficiency of 100% are accomplished. Operating systems with 5 M3/hr and 20 M3/hr methane processing capacity are currently and soon to be in operation.
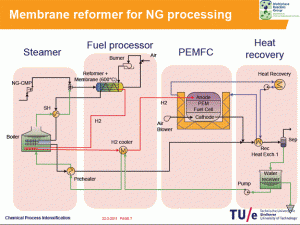
Trade-offs
Hydrogen recovery in the FBMR is 66%, which is lower than the 75% achieved conventionally. However, the unreacted CO can be used as fuel in the FBMR, and the lower temperatures require 25% less fuel to start with.
Lower operating temperatures gives better equilibrium conditions for hydrogen formation, but requires significantly more membrane surface area to achieve the desired flux. This change in hydrogen composition at equilibrium is the critical parameter, and leads to a higher efficiency but higher capital cost.
Greater conversion of CO to CO2 can be obtained by using some of the generated hydrogen in an autothermal reforming scheme. However, this results in lower efficiency due to an increase in non-power generating equipment. Conversions of 40-50% are achieved at the 43% efficiency mark. A reduction of efficiency to 34% (the base case) allows a 93% conversion to CO2, and complete conversion lowers the electrical efficiency to 28%.
Further Work
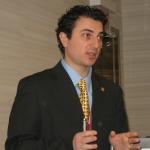
Ongoing experiments are dedicated to demonstrating the long-term stability of the membrane and to thoroughly understanding the trade-offs involved in operating efficiency and membrane quantity (capital cost). One of the sponsors of the research is HYGEAR in The Netherlands. For further information, contact Fausto Gallucci.